Article By Bryan Catley and his Alligator Lines Copyright ©
Note: When sanding you need to ensure you keep things square! Being plaster it is very easy to sand too much and end up with the edge not being square. Dry fit the corners and double check the bottom of the walls to ensure the structure will end being as square as possible.
The instructions suggest gluing the four walls together at this point but as with all the other kits I have constructed, I decided to actually paint and complete the walls as much as I could before doing this. I continue to find this approach gives me much greater control over things! Plus, for me anyway, it is much easier to paint the individual walls rather than the entire structure!
Window and doors come first. There are seven doors (four in the front and three in the back) and two windows (both in the front). Wood laser cut doors and window frames (along with some laser cut acetate for glass) are provided for the front. These openings all received a coat of flat black paint. The three rear doors are simply part of the molding so they were painted to actually represent the doors themselves.
Now to paint the walls themselves. Since this structure actually represents four different buildings they each received a color of their own. I was a little concerned about getting the lines straight between the buildings but it turned out to be easier than expected. There are edges in the molding that serve to delineate the buildings and they also make excellent guides for a small, soft brush!
Note: If you plan on using the chimneys and to use the same colors as you used for the walls, now would be a good time to do so!
Trim around the base was also painted in some contrasting colors and the top of the front wall received a coat of concrete colored paint. This left the wood doors and windows. They were first painted (on both sides to minimize possible warping and then removed from their container sheet.
Note: Make sure you don’t apply the paint too heavily. There is some fine detail etched into the doors and thick paint could well cover this up!
Dry fitting the doors showed a problem! The doors and windows for the right three stores fit just fine but the remaining door, while the correct height, was way too narrow for the left most (Pawn Shop) doorway! I decided to paint the door opening the same color as the building and then place the door in the center of the opening.
Next the appropriate pieces of acetate were located and glued to the back of the matching doors and window. (Very small dabs of CA glue were used for this task).
The doors and window were then positioned and, again using very small dabs of CA glue were glued into place. The left most window doesn’t have a frame. Instead a small piece of Plastruct glass block is provided for this opening. It did need a little trimming before it would fit.
The wall signs were next. They were given a very light sanding (to simulate age), carefully cut out and applied with glue. The glue used here was from a glue stick that was rubbed over the back of the signs.
Before the walls could be glued together it was necessary to glue some roof supports to the back of the walls. Only the two side walls were used and two strips of scrap from another kit were glued into place using a measured pencil line as a guide. Measure a suitable height and draw a line! Remember there are three “store dividers” to go on the roof so make sure you allow enough space for them!
With Randy’s Burgers I deviated from the instructions and also used CA glue. It ended up not being the best approach at all! This time I followed the instructions and used yellow glue and while it did take little longer the results were far superior!
Downtown Deco’s Addams Ave – Part 1
This is the second Hydrocal structure I have worked on, the first being Randy’s Burgers. I have to say that I am really glad for the experience of that smaller kit before tackling this one. As seems to be the case with these kits, while they do have an incredible amount of detail, it is the painting and detailing that makes or breaks them! The pieces also do not have the accuracy of laser cut kits (for obvious reasons) so be prepared to make adjustments on the fly! Note: Hydrocal is a cast plaster and can display a surprising amount of detail. The published footprint for this model is 4 x 2 inches but, it turns out, this is not correct! The actual structure measures 4 ½ x 2 ¼ inches! Not a huge difference but it does increase the overall area by almost 50% (8 square inches to 11.25 square inches) so it can impact things if you had planned on the published footprint. And this does not include any surrounding areas such as sidewalks, etc. A mix of yellow glue, CA glue and a glue stick were used during construction. The kit comes in a sturdy cardboard box and contains the four cast walls (well protected by bubble wrap), one large sheet of signs and awnings, some roof covering, a sealed plastic package of detail parts and the instructions. The detail parts include pre-cut pieces of styrene for the roof, signs and roofing (or “store”) dividers, a sheet of laser cut wood doorways and windows, a single strip of styrene for the sign supports, a stencil for an “end of the building” sign and four cast chimneys.
The instructions are printed on one side of ten 8 1/2 x 11 sheets of paper. They appear to be pretty much for all scales but there are some specific N scale notes. They start with an introduction to the kit on the first side and continue with specific instructions for this kit (including several black and white pictures) over the next four pages. The remaining pages cover tips on working with Hydrocal in general. They appear reasonably complete although I don’t recall seeing anything about the chimneys or the construction of the roof signs. Here is a link to the Fifer Hobby page for this kit (where I obtained mine) and here is the Downtown Deco page. As with most plaster cast kits there is a little flashing that will need to be trimmed and the wall ends may require some sanding to ensure a flush fit. The instructions imply you may have to trim the roof (but that turned out to be not necessary) and you definitely will have to cut the sign supports by yourself if you plan on adding the roof sign. Another thing you will need to do is provide some support for the roof on the inside of the walls. Of course, painting is a must with kits of this type and some care will be required. Once construction started the first thing was to clean any remaining flashing off the walls. The next thing was to sand the wall edges and bottoms to ensure smooth edges. Actually, this is a very important step since it will impact the appearance of the finished structure so do it carefully!
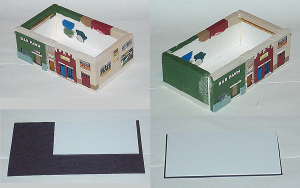
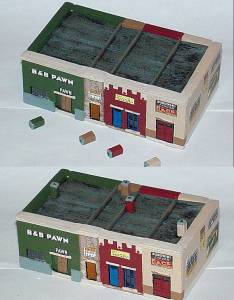
The first step was to glue one side wall to the front. A small amount of yellow glue was used and the two walls were left in a gluing jig for several hours. Once removed, I did use a small bead of CA in the corner as reinforcement. The other side wall was next and I used essentially the same approach. However, I did heed the instructions which state that since these plaster walls have absolutely no flexibility it is important to make sure the space at the back is exactly correct for the rear wall. To insure this was the case I used the back wall itself as a spacer while the second wall was drying. Once both side walls were in position a small bead of yellow glue was place on the inside of the rear of the side walls and the back wall was slide into position and received a little adjustment to insure it was where it was supposed to be. Placing the glue on the inside helps prevent any unsightly overflow when the wall is positioned. Once dry the structure was starting to look like a building! However, as is usual with these kits, the wall joints did need a little work. A toothpick was used to fill the joints with a small amount of joint compound. A finger insured a smooth finish. Of course, this means some touching up becomes necessary so this was done next. This left the roof itself. The supplied roof is actually a little small! It was pretty good from front to back but the end to end length was too small. In fact it was necessary to add another layer to the two roof supports to prevent it from just falling right through! Then using the roof piece as a template I cut an oversized piece of roofing material. They were then glued together. I used the glue stick for the majority but a couple of dabs of CA glue ere also used. Before getting the roof in place it was painted and weathered. Some dark gray was brushed on first followed by dry brushing of light gray and black. Since the roofing material was already black I never tried to cover it completely and if any ended up showing through, well that was OK! Once painted the roof was glued into position on the extend supports. The roofing material covered over any gaps very nicely!
Note: As it turns out I think that next time I work with a structure of this length I’ll add a couple of supports along the front and back as well. The extra support will make the roof much firmer. Now for the “store dividers”. The three supplied strips of styrene were first painted a dark gray. A second coat was obviously necessary. Once painted, they were glued into position, on the roof, using the wall paint color changes as a guide. So as far as the building itself goes the only thing left were the chimneys (which are never mentioned in the instructions). Since I hadn’t done it earlier, they were cleaned and each received a topping of light gray with a little spot of black to represent the actual opening. The main chimneys were then painted to match the building it would become a part of. Once dry they were glued onto the roof with random positioning. CA glue was used for this. At this time I also added four ventilators to the roof (one for each store). These are not part of the kit and are sold separately. They are from the Micro Engineering N Roof Vents & Fans packs. They are white metal and received a little black dry brushing before being glued into place. They were also placed pretty randomly but, if you plan to use the roof top sign, make sure you do not interfere with its positioning. This left a few more external signs and some awnings but first a little weathering was applied. This was done applying a thin black wash and then dry brushing it off. Before adding the awnings the external Pawn Shop sign was made. This sign consists of a pre-cut piece of wood, two paper signs (one for each side) and a piece of wire with which to form the support. First the two signs were cut from the paper using both scissors and a hobby knife. They were then glued onto the wood backing using a glue stick.
Note: Needle nose tweezers are a great help with this task! Once dry the piece of wire was formed around the curved top of the sign. This turned out to be easier than had been anticipated. Once done the wire was trimmed to the correct length and here, it is all up to you since there are no guidelines! The final step was to paint the edges of the sign and the support wire with a flat black paint. Once dry it was put aside until the Pawn Shop’s awning was installed. This was actually the next thing to be done! The kit provides a number of different awnings so you do have a choice. All are oversized (lengthwise, anyway) and require trimming. The chosen awning was cutout from the sheet of signs and trimmed to the correct length. Then, using scores from the back of my hobby knife, the front overhang and a small lip in the back were folded into position. Note: After scoring, use a straight edge on the score and gently lift he flaps with the edge of your hobby knife. It works very well! Using the narrow lip on the back the awning was glued into position using a very small amount of CA glue. After insuring the awning was at a suitable angle it was time to add the supporting rods. Once again the provided piece of wire was used for this task. The length was measured and two pieces were cut. Unfortunately, this pretty much used all the available wire! Only a very small piece was left over. Once the awning was dry the ends of the supporting rods were dipped in CA glue and positioned using my trusty needle nosed tweezers. Before moving on the Pawn Shop sign needed to be placed into position. Using the tip of my hobby knife a very small opening was “drilled” into the wall where the sign was to go. A small amount of CA glue held the sign in place very well. Of course, a little touching up was also in order! The awning for the Tattoo Parlor was next. I decided to follow the example and use the printed corrugated awning provided in the kit but separate from all the other signs. Once again it was too big and needed trimming. It also seemed to be pretty thin and flimsy so I decided to glue it to a piece of paper backing before actually using it. This worked well and it was glued into position using a small bead of CA glue.
This left the final awning for the liquor store. The awning was cut out and applied in the same manner as the Pawn Shop’s. However, there was no wire left for the supporting rods. I ended up using some very thin strips of wood from the container sheets of a previously constructed kit. This actually worked very well indeed! Two rooftop signs and the kit would be complete. A fair sized piece of styrene is provided for backing for the signs along with a small strip of styrene for the sign supports. Both were painted brown on all sides and the two chosen signs were glued to the backing using the glue stick. Once dry they were cut from the sheet using my hobby knife and a metal straight edge. The smaller one would end up on the front edge of the roof over the Tattoo Parlor while the larger one did require the building of some supports. However, the instructions provide no guidance on the construction of these supports whatsoever. I decided on two vertical supports directly on the back of the sign along with two other supports, with a cross piece, at an angle to provide the total support necessary. The vertical supports were cut and glued into position. The angular ones were also cut but, once again, there was not enough styrene stripping left for the desired crosspiece. For this, once again, I used a thin piece of wood from an earlier container sheet. The angular structure was now completed but it now had to be glued to the back of the sign! The question was, just where should it be positioned (and glued) so as to provide the support and keep the sign vertical! After some thought I came up with a method that worked very well! Using my gluing jig I placed the sign front down with the front legs up against a side. Then using a Popsicle stick and a square toothpick as a spacer up against the edge I positioned the angle supports which showed me exactly where they needed to be glued! Using this method the angular supports were glued into position.
Once dry the sign and its supports were removed and received some touch up paint where necessary. Both signs were then glued into position on the roof and the structure was finally complete! Note: The kit comes with a lot of signs and you can always add more to your hearts content! If you choose to do so you want to acquire some more styrene strips and/or wire for the supports. For those who have never done any scratch building this kit does provide a small taste of what it might be like. Not a big taste, just a small one which can also be avoided totally if desired! Back to How To